Vibro compaction is a ground improvement technique that densifies clean, cohesionless granular soils with a downhole vibrator. It’s a technique first developed by Keller in the 1930s that we’ve used on thousands of projects since.
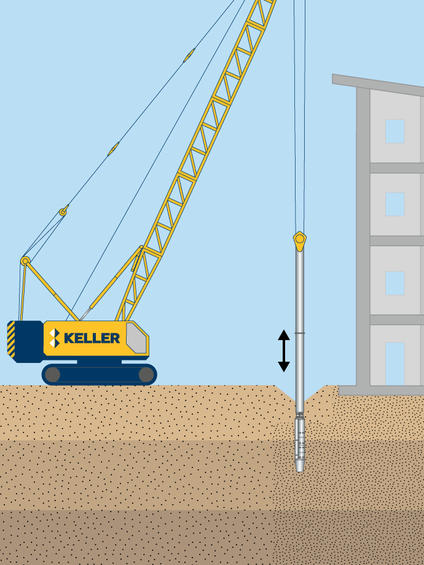
Common uses
Process
The Keller-made vibrators were first developed in the 1930s to compact granular, cohesionless soils at large depths from the ground surface, without any excavation. The Keller-made vibrators are far advanced today and, through research and development, we continue to develop vibrators that can compact soils efficiently with wide grids and large depths close to 50m.
A vibrator hung from a crane is lowered into the ground with penetration usually helped by water jetting. The energy from the vibration reduces the inter-granular forces between the soil particles, making them denser as the vibrator is raised in lifts. Sand backfill is then poured in from ground level to compensate for any decrease in soil volumes. More backfill is added and compacted and the vibrator is gradually removed until it has built up to ground level.
Vibro rigs can be fully instrumented with an on-board data acquisition system. Data from the system, such as amperage and lift rate, can then be recorded and displayed in real-time on an in-cab monitor. The production data can also be monitored from any Keller office by installing a mobile sim in the data recorder.
Advantages
Quality assurance
The vibro equipment we use is designed and manufactured by our in-house equipment manufacturer exclusively for use by Keller companies.
In-house quality production manager software enables us to capture and analyse data in real time and validate the performance of the ground improvement being carried out.
A variety of production parameters are generally logged during execution including depth, current, pull down force, uplift/pull down sequence, time and date and element number.
Field trials can also be used to verify column production parameters, along with static load tests, single or group, column material compressive strength tests, and column diameter verification.